Apr 22, 2024
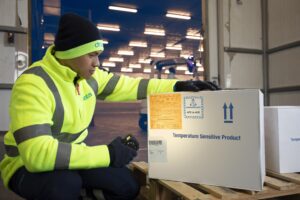
There are a number of primary considerations when handling dangerous goods. Firstly, communication throughout the transportation chain is extremely key in ensuring that any hazards and potential risks are well managed. Alongside that, continuous monitoring and supervision will identify and address any potential hazards promptly.
Handlers must strictly adhere to international and local regulatory requirements and ensure that the goods are properly and safely packed to withstand any potential hazards during travel, such as leaks, spills and drops.
They must hold all accurate and complete documentation detailing the dangerous goods and any special handling requirements, keep on top of training to understand the risks involved, and ensure they understand all current regulations.
Handlers must also provide the space to segregate incompatible goods during storage and transportation, particularly at stations where cargo companies handle high volumes of dangerous goods.
Risk assessment is a key consideration during the handling process, ensuring that handlers have contingency plans in place for any emergency response. This is critical to swiftly address any incidents that may occur, It having the correct firefighting equipment in place.
“In addition to training and segregation, our role of mitigation starts from a strict acceptance criteria to check for improper packaging and/or identify undeclared dangerous goods,” Barry Shields, dnata’s Manager of Cargo Operations – Special Products, said.
“Of course, risk assessment and monitoring of shipments plays a big part.
“Collaboration and information sharing: especially with the United Arab Emirates (UAE) Regulator General Civil Aviation Authority (GCAA) and our partner carriers, to share information and best practices for managing dangerous goods, allowing for continuous improvement and updates on safety measures.
“In the UAE, we also have a backlisting program, run by the GCAA, whereby repeat offending DGR agents who fail to follow regulations have their DGR licences revoked.
“Standardisation is crucial in promoting safety, compliance, and efficiency within the airfreight industry.
“To ensure that we follow clear guidelines, standardisation minimises the risk of accidents and incidents. This enables smooth cross-border trade to comply with consistent standards, regardless of their origin or destination.
“It also reduces the likelihood of non-compliant penalties and overall, eases the cargo handling process chain to ensure a safe operation and inherent risk to air cargo transport.”
READ: Emirates shakes up senior management team
Avoiding e-commerce risks
The rise in e-commerce has inevitably resulted in an increase in the volume of goods being shipped, containing lithium batteries. Therefore, adjustments in the infrastructure to handle them have also needed to be modified.
However, there are increased safety concerns, especially around hidden products and shippers without sufficient expertise entering the market. The increasing volume of products with improper packaging has also increased.
“The main challenges of handling lithium batteries are their potential to overheat, catch fire, or explode if damaged or incorrectly handled,” Shields stated.
“To overcome these risks, the responsibility mainly falls with the shipper to ensure correct packaging requirements are met, such as sturdy packaging and insulation to minimise physical damage. This is specified by IATA, and compliance is paramount.
“Shippers must make sure that labelling and documentation are fully completed for awareness of the contents with appropriate warning symbols and emergency contact.
“We are looking at ways in which we can detect and identify hidden dangerous goods beyond just relying on the shipper and gaining a declaration,” Shields explained.
“This includes training our staff to recognise potentially dangerous items through invoices or packing lists and package markings.
READ: Autonomous drones propel dnata’s cargo services to new heights in Dubai
Prepared for anything
dnata is strategically expanding its facilities to cater to the escalating demand for the movement of lithium batteries. Through robust engagement and collaboration with all stakeholders, the cargo handlers prioritise investments in infrastructure, technologies, and products to bolster efficiency, productivity, and customer value.
Recently, dnata achieved certification with IATA’s CEIV lithium battery program, marking a significant milestone. As the first ground services provider to certify 11 of its worldwide stations, the company undertook a comprehensive audit process to ensure adherence to the stringent safety standards. Stations in Australia and Pakistan led the way, followed by Singapore, Belgium, the UK, and the UAE.
“At the core of our operations is a steadfast dedication to delivering the highest quality and safest services consistently,” Shields said.
“Safety remains paramount in every aspect of our operations for all dangerous good products and lithium batteries only being one of them, reflecting our unwavering commitment to service excellence and customer satisfaction.”
In the event of an emergency involving dangerous goods, dnata has Dangerous Goods Responders (DGR) who will be alerted to any incident that involves a dangerous goods package.
This could be as little as a leak, and process around that to isolate the incident, use fire drill kits in every warehouse to contain any leak and prepare the area and documentation for the arrival of emergency services.
This will also include the evacuation of the area if it is deemed unsafe or a substance of a nature that could cause injury or inhalation issues.
Following the incident, a report will be raised in the company’s safety hub portal and additionally with the GCAA to initiate an investigation to determine the root cause and identify any corrective actions needed to prevent similar incidents in the future.
“Our staff can only handle dangerous goods if they have the required certification,” Shields stated.
“This is closely monitored by our training departments, and staff are removed from the roster if they lapse.
“For any updates on changes to the manual and/or process, our staff are briefed through a digital document which is electronically acknowledged and tracked monthly by our S&P teams for adherence.”
The post Safe and secure dangerous goods transportation appeared first on AIR CARGO WEEK.
Go to Source
Author: Edward Hardy